Spring supports are installed when the vertical movement of the pipe is such that solid support is not suitable, either because the pipe lifts off the support or the downward movement is restrained, thus setting up large stresses in the line and/or high loadings on equipment nozzles.
Types of spring supports:
Variable Spring supports
Constant Spring supports
Both types of spring are pre-compressed so that they exert a specified upward force on the pipe. Ideally this force is equal to the weight of the pipe (plus contents) the spring is intended to support, thus imposing minimum weight loading on adjacent supports or equipment. The difference is that as the pipe moves from the installed to the operating position the force exerted by a variable spring alters as the compression on the coils is either increased or reduced where as that of constant unit remains virtually unaltered
Variable springs are preferred to constant on economic grounds, being cheaper by a factor of between 2 and 3 than an equivalent constant unit. Generally variability at spring adjacent to strain sensitive equipment such as pumps, compressor and turbines is limited to 20%. Where a suitable variable spring cannot be specified, a constant unit is used.
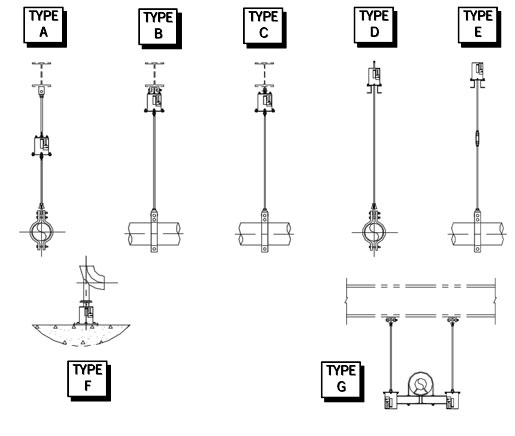
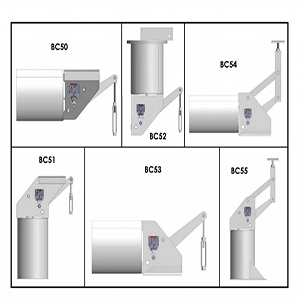
Location of spring supports
Spring supports specified during the flexibility review are located on the Stress Sketches and it is the Pipe Support Designer’s responsibility to reflect this in the design. Generally spring locations are governed by practical considerations such as the location of steelwork rather than optimum support positions. However, special structures may be erected for specific purposes eg. spring supports directly above top discharge nozzle of pumps.
Spring Deflections
Variable springs are rated for deflections applying to normal operating conditions. Additionally, the spring travel must be sufficient to cater for all other expansion conditions (design, start-up, shut-down etc). The spring variability for these conditions is reviewed and the springs selected so that excessive loading on adjacent nozzles is avoided.