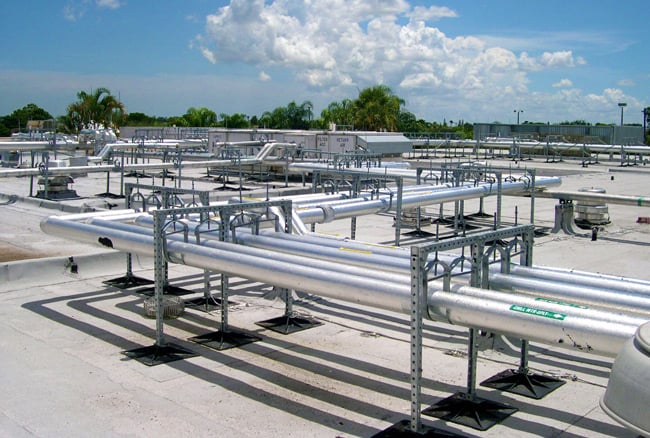
The design of support structures and foundations is aimed at withstanding the weight of the pipelines and other pipe loads acting on the structure, such as friction loads, anchorage loads, and wind loads at guide devices. If the pipeline system primarily handles natural gas, the support structure design may be optimized only for operational loads and not for hydrostatic loads. Besides, crude oil and other petroleum products are lighter than water, thus the maximum contained weight occurs during the hydrostatic test. Because hydrostatic test loads can be much higher than operating loads, particularly for large-diameter pipes, the support structures may not be sufficient to bear the hydrostatic test loads.
In such cases, designers can provide temporary supports during the hydrostatic test, and the design documentation, including the stress analysis report, should clearly indicate that additional temporary supports are required for the hydrostatic test.
When a multitude of pipes are supported by structures such as pipe racks, designers commonly consider worst-case scenarios when designing the supports and associated foundations. This typically means one pipe undergoing a hydrostatic test at a time while the rest of the pipes carry normal operating loads.